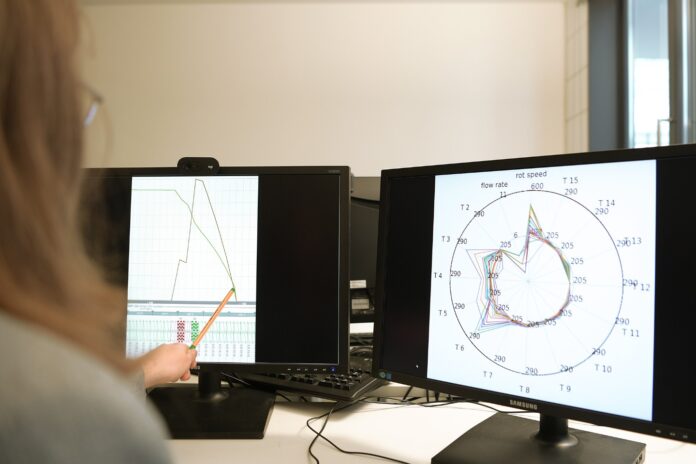
Digitale Zwillinge gelten in vielen industriellen Prozessen als Schlüsseltechnologie. Für die Kunststoffindustrie haben Forschende des Fraunhofer-Instituts für Techno- und Wirtschaftsmathematik ITWM in Kaiserslautern ein Machine-Learning-Tool entwickelt, das mithilfe eines Digitalen Zwillings die optimalen Prozesseinstellungen ermittelt. Der Digitale Zwilling berechnet ausgehend von den gewünschten Produkteigenschaften die benötigten Einstellungen des Extruders. Dadurch können Unternehmen Zeit und Ressourcen sparen und gleichzeitig die Qualität ihrer Produkte steigern.
Ein zentraler Prozess in der Kunststoffindustrie ist die Extrusion. Dabei wird Kunststoff als zähe Masse unter hohem Druck und hoher Temperatur durch eine formgebende Öffnung gepresst. Ziel ist es, bei möglichst geringem Energie- und Materialaufwand ein möglichst hochwertiges Produkt zu erstellen. Das können zum Beispiel Kabelummantelungen, Rohre für den Bau, Folien oder Wärmedämmplatten sein. Damit die gewünschte Qualität der Produkte erreicht wird, spielen diverse Prozesseinstellungen am Extruder eine Rolle, wie Drehzahl, Durchsatz und Temperatur der Heizelemente. Die Qualität des Produktes wird beispielsweise bestimmt durch die Schmelztemperatur, den Druck oder die Verweilzeit.
Um die optimalen Werte der Prozesseinstellungen zu finden, greifen die Betriebe meist auf Erfahrungswissen zurück. Spätere Anpassungen nach dem Prinzip »Trial & Error« vorzunehmen, ist aufwendig und führt zu Materialausschuss und hohen Energiekosten. Basierend auf Methoden des Machine Learnings, Künstlicher Intelligenz sowie statistischer Datenanalyse haben Forschende des Fraunhofer ITWM auf Grundlage von Versuchsdaten des Projektpartners Fraunhofer ICT eine Software-Lösung entwickelt, die die optimalen Einstellungen eines Extruders ermittelt.
Datenwolken erweitern reale Versuchsdaten
Für Machine-Learning-Verfahren werden sehr viele Daten benötigt. »Diese Daten allein über Versuche zu generieren, ist viel zu aufwendig,« erklärt Julia Burr, Expertin für datengetriebene Modellierung am Fraunhofer ITWM, die Herausforderung, die sie zunächst angehen musste. »Wir haben dann eine Möglichkeit entwickelt, mithilfe einer Simulationssoftware aus wenigen Messdaten eine ausreichend große Datenwolke aus Mess- und Simulationsdaten zu generieren.« Zu Beginn entstanden im Projekt deshalb zunächst reale Versuchsdaten am Fraunhofer ICT. Anhand der durch Simulationen erweiterten Datenwolke erstellte Burr anschließend einen Digitalen Zwilling.
An den Strompreis gekoppelte Produktion
Im Rahmen des Projekts »ENERDIG – Energiemanagement 2.0, Digitalisierung, KI und Optimierte Prozesse« haben die Forschenden ihre Software-Lösung weiterentwickelt. Mithilfe des digitalen Zwillings können so präzise Einstellungen vorgegeben werden, die zu einem netzdienlichen Stromverbrauch führen. Falls viel Energie eingespeist wird oder der Strompreis günstig ist, wird der Durchsatz hochgefahren. Die passende Drehzahl und Temperatur der Heizelemente werden vorgegeben, sodass die Qualität des Produkts sichergestellt wird. Ist der Strom teuer, so können Einstellungen vorgeschlagen werden, die einen niedrigen Energieverbrauch bei gleicher Produktqualität sicherstellen. »Das Unternehmen stärkt damit nicht nur seine Marktposition durch günstigere Produktion, sondern liefert einen wichtigen Beitrag zur Netzstabilität und dazu, den Anteil der erneuerbaren Energien zu erhöhen,« Julia Burr.
Maßgeschneiderte Lösungen für Unternehmen
In der Praxis sichtet das Team gemeinsam mit einem Partnerunternehmen vorhandene Daten und entwickelt eine Datenerhebung, um mit minimalen Kosten und kleinstmöglichem Aufwand die vorhandene Datenbasis zu ergänzen. Falls nötig, passen die Forschenden ein Simulations-Tool individuell an die betreffende Maschine an, um weitere Daten zu erzeugen. Anschließend erstellen sie einen Digitalen Zwilling und mit dessen Hilfe berechnen sie die benötigten Einstellungen.
Darauf aufbauend entwickeln sie eine Steuerungsstrategie. Die Ergebnisse werden in ein Assistenzsystem gegossen, damit die vorgeschlagenen optimierten Stellgrößen direkt vor Ort an der Maschine zum Einsatz kommen. Dabei wird der/die Maschinenführer:in nicht ersetzt, sondern ihm wird eine Entscheidungsgrundlage geliefert.
»Denkbar ist es auch, schon die Herstellenden von Extrudern in den Prozess einzubinden und die Maschine von vornherein mit Funktionen der Künstlichen Intelligenz auszustatten. Damit kann unser Tool schon von Beginn an vermeidbare Kosten durch Zeit- und Materialersparnis verhindern,« so Julia Burr zu den Einsatzmöglichkeiten ihrer Entwicklung.
—————–
https://www.facebook.com/wissenschaftkl
Quelle Text/Bild:
Fraunhofer-Institut für Techno- und Wirtschaftsmathematik
Fraunhofer-Platz 1
67663 Kaiserslautern
www.itwm.fraunhofer.de
Kaiserslautern, 12.11.2024